徐州海华电气有限公司
HXL 智能主令控制器说明书
目录
一、设备简介。。。。。。。。。。。。。。。。。。。。。。。。。。。。。。。。。。。。。。。。。。。。。。。。。。。。。。。。1
二、设备性能。。。。。。。。。。。。。。。。。。。。。。。。。。。。。。。。。。。。。。。。。。。。。。。。。。。。。。。。1
三、技术参数。。。。。。。。。。。。。。。。。。。。。。。。。。。。。。。。。。。。。。。。。。。。。。。。。。。。。。。。
四、工作原理及操作方法。。。。。。。。。。。。。。。。。。。。。。。。。。。。。。。。。。。。
五、调试方法。。。。。。。。。。。。。。。。。。。。。。。。。。。。。。。。。。。。。。。。。。。。。。。。。。。。。。。。
(一) 安装前调试。。。。。。。。。。。。。。。。。。。。。。。。。。。。。。。。。。。。。。。。。。。。。。。
(二) 现场调试。。。。。。。。。。。。。。。。。。。。。。。。。。。。。。。。。。。。。。。。。。。。。。。。。
六、注意事项。。。。。。。。。。。。。。。。。。。。。。。。。。。。。。。。。。。。。。。。。。。。。。。。。。。。。。。。
(一) 安装时注意事项
(二) 接线时注意事项
(三) 操作注意事项
附页:。。。。。。。。。。。。。。。。。。。。。。。。。。。。。。。。。。。。。。。。。。。。。。。。。。。。。。。。。。。。。。。
一. 设备简介
智能主令控制器,是众多电气工控系统专家经过数年努力而研制成功的一种新型智能主令控制器。智能主令控制器由绝对值编码器、主控单元组成。绝对值编码器安装在现场,与受控设备传动轴柔性连接。主控单元安装在控制室或操作室内,由Siemens操作面板TD 400、S72200 PLC等组成。编码器和连接电缆将现场位置信号送至主控单元,共同构成智能主令控制器。它采用先进的数据检测和分析技术从本质上改变了LK系列旧式主令的工作原理,形成了一个LK主令更新换代的自动化产品。
该智能主令控制器自从投放市场以来,就以其运行可靠、保护功能齐全、分辨率高、抗干扰能力强、响应速度快、调整方便迅速、人机界面友好、使用范围广泛等优点而赢得了广大用户的青睐,尤其在高炉主卷扬、料线、料钟、石灰竖炉卷扬、炼钢炉氧枪控制、转炉倾动、混铁炉倾动、焦化设备平煤机、推焦机等自动化工业控制场合被广泛应用。该主令取代老式凸轮主令控制器以后,取得了满意的使用效果和显著的经济效益,在运行中几乎做到了零故障率。
二.设备性能
智能主令控制器具有运行可靠、响应速度快、分辨率高、调整方便迅速、可在运行中调整、全数字显示、远程通信、多种保护功能等优点。 (1) 运行可靠。该主令设计思想是用弱点控制强电,用程序逻辑代替机械凸轮的动作,以无触点代替有触点,这样就避免了许多机械故障,从而提高了主令控制器运行的可靠性。 (2) 反应速度快。主令由于采用可编程控制器进行控制,故其响应速度非常快,响应速度可达微秒级。 (3) 分辨率高。该主令的分辨率由编码器的分辨率决定,可达到毫米级,精度非常高,能适应需要精确定位和精确限位控制的场合。而老式主令采用凸轮闭合、断开触点,其精度低,不能适应自动控制过程精确控制的需要。 (4) 调整方便迅速。该主令的调节无需任何工具,仅需对TD 400操作面板操作,即可达到调整的目的,与老式主令相比,可以节约时间,减少劳动强度,从而提高经济效益。 (5) 运行中调整。该主令控制器可在设备运行状态中进行调整,设备不必停车即可对控制信号的输出位置通过TD 400操作面板进行微调。 (6) 数字显示。在被控物体运行期间可以方便地从操作面板TD 400上观察出其所处的位置。 (7) 远程通信。该主令具有远程通信功能,可以直接和其他控制系统(如: PLC系统、工业控制网络系统)相连接。 (8) 保护功能齐全。该主令设有过速保护、脱轴、倒转保护。 三.技术参数
1.主控单元技术参数
电源电压允许范围:85-264VAC,47-63Hz(外部提供)
输出类型: 继电器、干触点(PLC本身继电器)
最大负载电流: 2A/点(PLC本身继电器输出),
5A/点(外接继电器输出)
输入点数: 8/10点(可选)
输出点数: 10/16点(可选)
程序保存时间: EEPROM永久保存
2现场变送单元技术参数
变速比: 1:1
最高旋转速度: 1000r/min
3.主控单元到现场变送单元距离:
280m (如主控单元到现场编码器距离较远,
可以选用Profibus总线编码器) 。
四. 工作原理及操作方法
1.工作原理
当受控设备运动时,受控设备通过现场变送单元的传动机构带动编码器一起旋转,编码器将受控设备的位移转化成格雷码(其转化精度视现场需要而定),送到可编程控制器(PLC)的输出端,PLC将采集到的格雷码进行译码、累加等数学运算处理,并将受控设备的位移通过操作面板TD400中所显示的“当前位”间接的表示出来,同时把“当前位”与TD400中显示的可调的设定参数相比较,在合适的位置发出相应的控制信号,从而实现受控设备的精确定位.另一方面PLC还对采集到的信号进行分析,判断受控设备是否出现超速、零速或溜车等故障,如出现故障立即发出停车信号并报警,以防止意外事故的发生。
2.卷扬系统应用操作示例
数字概念:(以单斗上料小车为例)
小车在斜桥上运行的同时,同步带动编码器旋转,PLC采集到的是一系列的编码,确定了“原点”以后,小车在斜桥上整个行程中任一位置都在PLC中有一个唯一的相对于“原点”的编码,这些编码按十进制整数在-32767-+32767之间连续排列,这些编码都反映了小车当前位置与原点之间的位置关系(编码数),也就是用数字反应了小车在斜桥上的实际位置,通过精度(mm/点)可以计算出当前位置距原点位置的距离(单位:米)。
斜桥可以理解为一个斜方向的坐标轴,以“原点”为坐标原点,从小到大范围是-32676-+32676。
“原点”是一个参考点,对应小车在斜桥上整个行程中一个具体的物理位置,在PLC中的编码为“0”,根据需要可以把小车在行程中任一位置所对应的编码改为0,设定为原点(一般把斜桥底部小车装料位置设为原点),TD200上所显示的“当前位”及其他设定的限位都是以“原点”为参考点的。当“原点”所对应的实际物理位置发生变化时,“当前位”及其他限位所反映的实际物理位置都会发生相应变化。
“当前位”:确定了原点以后,小车所在斜桥上实际位置对应的编码我们称之为小车的“当前位”,它反映了小车当前所在斜桥上以参考点“原点”为坐标原点的位置(编码数)。如小车在“原点”位置时对应的编码时“0”,我们称“当前位”是“0”,相对于原点的距离是0点;小车运行到斜桥中间时,对应的编码是“1000”,也就是与原点“0”的距离是1000个点。小车在运行当中位置不断变化,“当前位”也随之不断变化。
精度计算:计算当卷筒旋转一周时旋转编码器转几周,假设一卷筒直径为1200mm,当卷筒旋转一周时旋转编码器也旋转一周,由于旋转编码器旋转一周为256个码,所以主令精度为3.14×1200/256≈15mm。也就是“当前位”每增加1个点,小车实际运动约15mm;每减少1个点,小车反向运行约15mm。
限位区间:区间是指从小到大的一个数字区间,“当前位”编码在某一范围内时,主令控制器输出点接通,参与系统控制或连锁,起到限位的作用,这一范围用两个数字表示。例:当Q0.0设为“10->1100”时,则“当前位”编码在大于10并且小于1100的区间范围内时Q0.0接通,不在这一范围内时Q0.0断开。
下例中,当Q0.0、Q0.1、Q0.2、Q0.3 、Q0.4、Q0.5分别作为系统中的常闭下限位、常闭上加速、常闭下减速、常闭上减速、常闭下加速、常闭上限位使用。
当小车上升时,“当前位”编码连续增加,“当前位”编码上升到大于200以后“上加速”限位Q0.1对应接点断开。控制系统控制小车以高速运行,上升到大于1500以后“上减速” Q0.3断开,控制系统控制小车以低速运行,上升到大于1800时,“上限位” Q0.5断开,控制小车停止。
当小车下降时,“当前位”编码连续减少,“当前位”小于1600时,“下加速”限位Q0.4断开,小车被控制以高速运行,小车继续下降,“当前位”小于300时,“下限速”限位Q0.2断开,小车被控制以低速运行,下降到小于20时,“下限位” Q0.0断开,小车停止运行。
例:
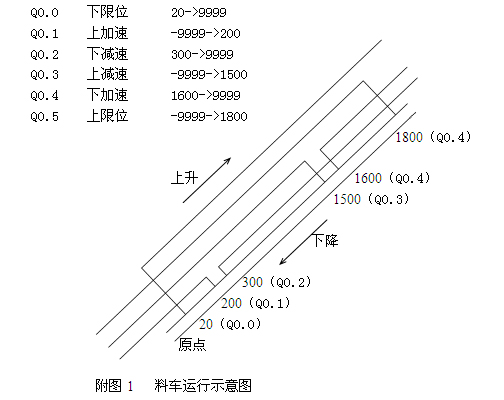
五.调试方法
智能主令控制器的调试一般分为两部分:
(一) 安装前的调试:
1、 设备安装以前,首先对设备进行外观检查:打开机箱查看外观是否异常,有无碰撞痕迹,螺丝、接线是否有松动现象,按照图纸检查线路。重点检查电源线路,是否有短路、松动等现象。
2、 打开现场变送单元箱,查看编码器连轴器顶丝是否顶在了平面上及是否上紧。
3、 上电检查:
1) 按照图纸把现场变送单元与主控单元连接起来,然后接通电源。查看PLC是否有电;上电几秒钟后首先检查TD400文本显示器显示的内容是否正常,应该是说明书附页信息表中的F1键对应的内容;如不正确可查看PLC运行指示灯是否亮,如STOP指示灯亮,请打开PLC盖板拨动小开关到RUN位置。
2) 在TD400显示信息正常的情况下,按下“原点设定”并设定原点(参考附页)使当前位显示为“0”,然后缓慢转动现场变送单元箱出轴,观察当前位数字是否依次增加直到255以上,在同一方向旋转时数字是否有不连续、上下波动现象,如有,应检查现场变送单元到主控单元10芯线接线是否正确。
3) 观察旋转方向与数字变化方向是否一致。如:按参考小车(两个小车时用其中一个为参考小车)上升的方向手动旋转现场变送单元箱出轴时,“当前位”的数字应增加。
4、 新型智能主令控制器连接方法和旧式主令连接方法相同。根据用户不同的使用场合先确定设备运行的精度,一般可在10~20mm之间选择,之后根据所确定的精度,选择现场变送单元的变速比及现场变送单元与受控设备连接部分的变速比。现场变送单元与受控设备之间连接方法一般有3种:①齿轮连接、②链轮连接、③滑块连接。具体用哪一种方式连接根据用户现场情况确定。
(二) 现场调试
现场变送单元和主控单元安装后:
1、 检查接线、电源等级是否正确(与安装前调试方法相同);
2、 观察连接部分咬合是否完好;
3、 限位粗调:
1) 把小车点动停止在下限位,设定原点,使“当前位”数字变为“0”。
2) 手动低速运行小车、手动停止让小车从斜桥底部装料位置运行到斜桥顶部倒料位置,观察并记录TD400所显示的“当前位”的变化范围,比如当小车在斜桥底部底部装料位置时对应的“当前位”为“0”,当小车在斜桥顶部倒料位置时对应的“当前位”为2000时,如上、下限位都为常开点到位闭合,可以设定上限位数值位1000-+∞( ∞可用比2000大很多的数值来表示,如9999),下限位为-∞-﹥500( - ∞可用比0小很多的数值来表示,如-9999)。设定原则为即使上、下限位没有起作用也有足够的安全距离来手动紧急停车),低速运行小车观察当“当前位”变化到大于1000时,上限位对应的输出点有没有信号,小车有没有自动停止,如小车没有自动停止应手动紧急停止小车并检查线路;同理当“当前位”变化到小于500时,下限位对应的输出点应该有信号,小车也应该自动停止;如果上、下限位信号都正常,小车到上、下限位后都能够自动停止,此时观察并记录小车到上限位及下限位后实际停止时TD400所显示的“当前位”为多少,此数值与设定的上、下限位之间的差值可作为小车低速上升和低速下降时的惯性量的参考值。
3) 让小车上下来回运行,自动停车,准确无误后再根据原先所记录的小车从斜桥底部到顶部“当前位”的变化范围上,把上、下限位逐步调整到合适的位置(上限位离实际倒料位置有三四米左右,下限位离实际装料位置有三四米左右),初次调整后一定要逐步接近并调整到该位置,以免掌握不好位置而使小车掉道。
4) 粗调好上、下限位后,如小车有加、减速,设置加减速调速区,手动低速运行小车使小车运行到所设置的加、减速区间内观察其对应的输出点有没有信号,如正常,高速运行小车,观察当“当前位”变化到所设置的加、减速区间内时,小车有没有自动变速。如没有起到自动变速的作用,紧急停车并检查线路。
4、限位细调:
经过粗调后,保证每个限位都起到相应的作用,让小车上下来回运行,自动变速、自动停车,准确无误后再把各限位逐步调整到所需要的位置,初次调整后一定要逐步调整上下限位的位置,以免掌握不好位置而使小车掉道。
5、 严格注意小车运行方向,参考小车上升时“当前位”数码增加,下降时“当前位”数码减少。调试时现场一定要有紧急停车手段,建议现场安装紧急停车安全开关,以便出现错误时能随时停车。
6、 带负荷试车:观察小车上升到上限位实际停止时是否能倒尽料,小车下降到下限位实际停止时装料位置是否合适,再进行上、下限位的微调。
7、 正常投入运行后要多观察小车的到位情况,随着钢丝绳的延伸变形,要在初次使用的几天内细调几次。
六. 注意事项
1、安装时注意事项
1)为保证通风与保养维修,周围要留有一定位置;不要安装在露天的地方,现场变送单元与受控设备连接的地方要安装防护罩。
2)现场变送单元与受控设备出轴连接时,一定要注意同心或安全咬合,避免因机械问题造成事故。
2、接线注意事项
1)现场变送单元与主控单元之间距离较远,需要另外敷设电缆时,必须选用屏蔽电缆。
2)控制电缆应避开高压线和动力线,尽量单独走线,加防护钢管。
3)主控单元电源线应选用标称截面为1.5~2.5 的导线。
4)控制电缆导线应选用标称截面为0.5~1.5 的导线,若敷设距离较远,必须选用屏蔽电缆。
3、操作注意事项
1)受控设备运行过程中严禁设定原点。
2)每次主令控制器失电后,须确保卷筒不转动;如果卷筒在控制器失电后有转动,再次上电后,应使料车回到原点位置,观察当前位显示值是否为零,若不为零,则需重新进行原点设定。
控制原理:当前值大于等于限位定值时,相应的电器断开,当前值小于限位设定值时,相应的继电器闭合。
1. 控制原理示意:
假设1号车从原点到小车上停止点为60米,即行程设定数值,
一减,即第一减速点(KA1)设40米
二减(KA2)设45米
低减(KA3)设50米
顶点(KA4)设59.70米
超限保护点(KA5)设60.30米
则1号车上升到40米时,KA1断开;上升到45米时,KA2断开;上升到50米时,KA3断开;到59.70时,KA4断开,小车惯性前行0.30米停止。
2号车下降到59.70米时,KA12继电器闭合;下降到50米时,KA11闭合;下降到45米时,KA10闭合;下降到45米时,KA9闭合。
一般情况,1号车、2号车行程应对应相等;如不等,一般误差不应超过10~20cm。厂家可以选择1个车作为行程设定数值,每一个车的超限保护点应超过行程设定值。
警告1:数据输入后初期调试运行时,应严格注意小车运行方向,当小车上升时,当前位置数值应递增,另一辆车的数值应递减,调试现场一定要有紧急停车措施;另外初调时,应低速手动运行,一方面小车运行时,观察所设点是否可行,另一方面,可以从面板上看到行程设定值是否准确。
警告2:小车在运行时严禁更改零点,初次设置减速点时,应小一些。
A.主控单元箱继电器对应点和接线方式:
(咯吱封底)
接通电源20秒,面板TD400显示
1.小车位置: 0.00米
2.小车位置: 0.00米
当前速度: 0.00米
按ESC,面板TD400显示
限位设定:
实时参数:
初始设定:
按上、下键选择“零点校正”,按enter键,面板显示:
编码系数:0.00cm/n
行程设定:0.00米
当前位置:0.00米
零点校正密码: (=19)
再按enter键,面板显示:
输入密码
密码**** (=0009)
密码****用上下键输入,每输一位要按enter键一次,完毕返回。
此时,TD400面板显示
编码系数:0.00米
行程设定:0.00米
当前位置:0.00米
零点校正密码:
同时,“编码系数”后出现闪动光标,即可用上下键输入,按enter键确认;
光标移到下一行“行程设定”,用上下键输入,按enter键确认;
依照同样的方法,输入零点校正密码。
(说明:编码系数=主卷扬直径×3.14/1024
例:主卷扬直径=180cm
则,编码系数=180×3.14/1024=0.55cm/n
编码系数输入完毕确认后,当前位置即显示一个数值,如204.62米。
行程设定=小车上停止点数-小车原点数
当原点数为0时,小车上停止点数即为行程数据。
当前位置调零方法:
1号车处在原点后,将当前位置数据加零点校正数据,输入到零点校正区,按enert键后,当前位置应变为0.00米;
例:204.62+0.00=204.62米,用上下键输入,按enter键确认即可。
2号车处在原点后,输入零点校正密码:19,按enter键后,当前位置变为0.00米,此当前位置为2号车0位。)
全部输完后,光标不再闪动,按esc键,画面返回。
限位设定:
实时参数:
初始设定:
选中“限位设定”,按enter键,光标即出现在画面中。光标在哪一行,哪一行即可输入,完毕后按enter键确认。光标消除后,按上下键翻到下一画面,按enter键确认。全部输入完毕后,按esc键返回画面
限位设定:
实时参数:
初始设定:
用上下键选择“实时参数”后,按esc键返回画面
1 小车位置: 0.00米
2 小车位置: 0.00米
当前速度: 0.00米
所有设置即告完成。
如果参数需要调整,即可按照上述方式进行,完毕后要使画面返回最初画面
1. 小车位置:0.00米
2. 小车位置:0.00米
当前速度:0.00米
B. 主控单元箱1、2号车按下面区分,调试参照上述步骤。
注意:应定期(2个月)对变送单元内的联接进行维护保养。
主要元器件
序号 |
名称 |
型号 |
生产厂家 |
1 |
中间继电器 |
MY2NJ |
欧姆龙 |
2 |
触摸屏 |
6AV6640
|
西门子 |
3 |
PLC本体 |
6ES7214
|
西门子 |
4 |
数字量输出模块 |
6ES7222
|
西门子 |
5 |
编码器 |
EAB50 |
宜科 |
6 |
高炉卷扬机械保护装置 |
LH-ZN50BH7 |
海华 |
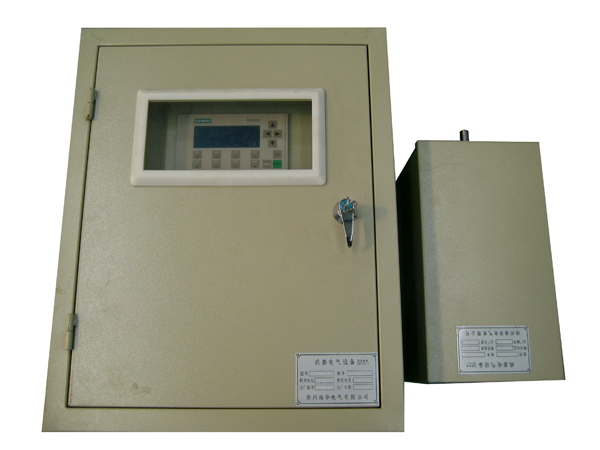
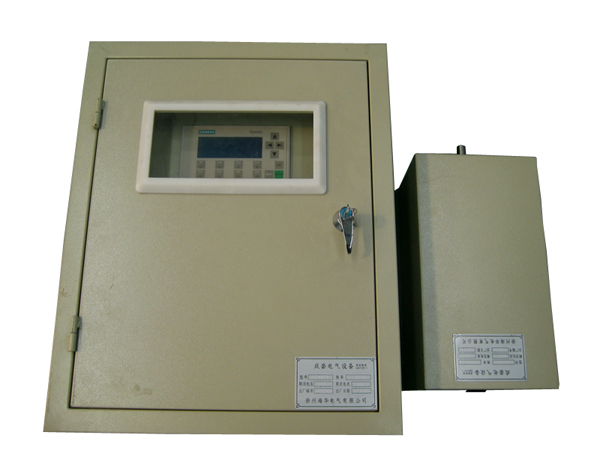
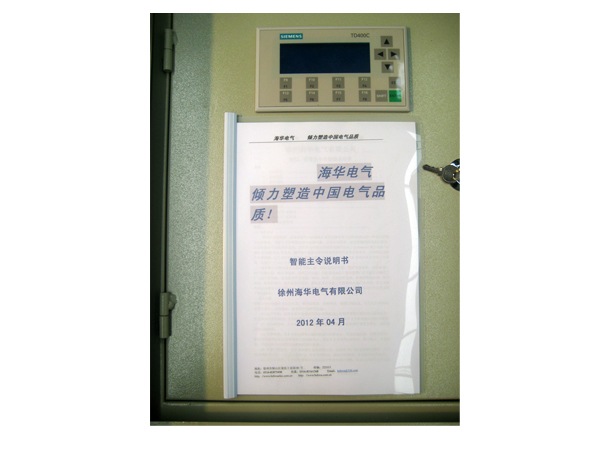
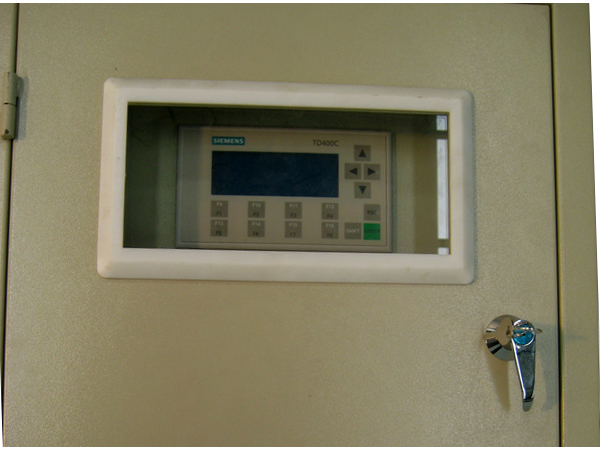
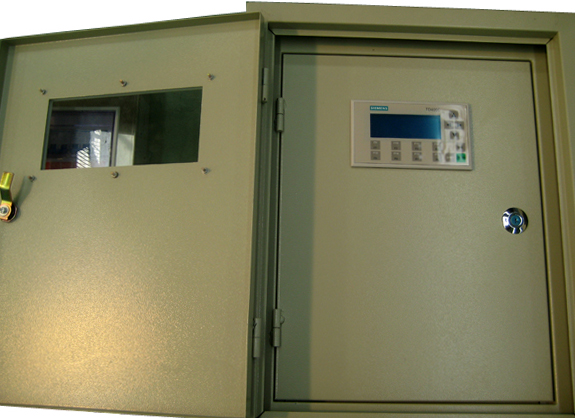
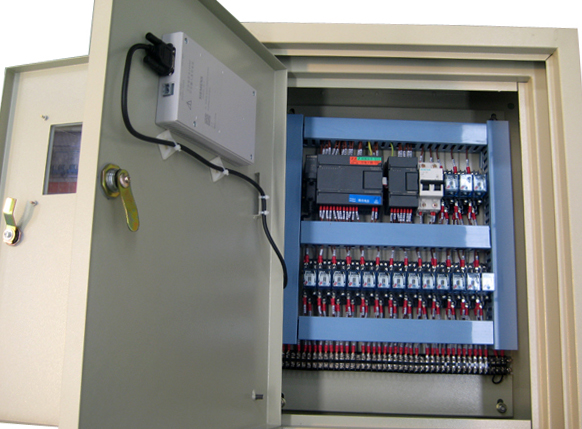
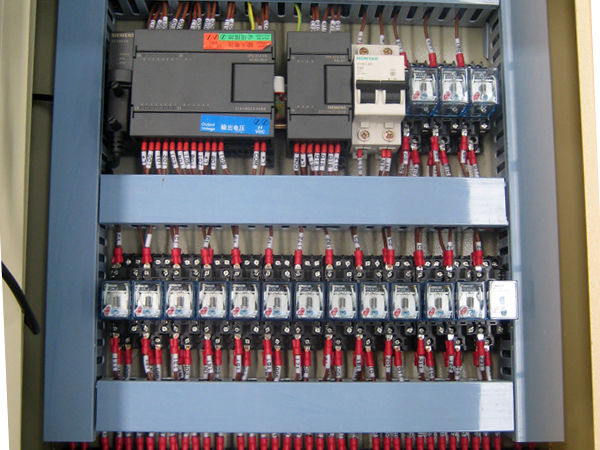
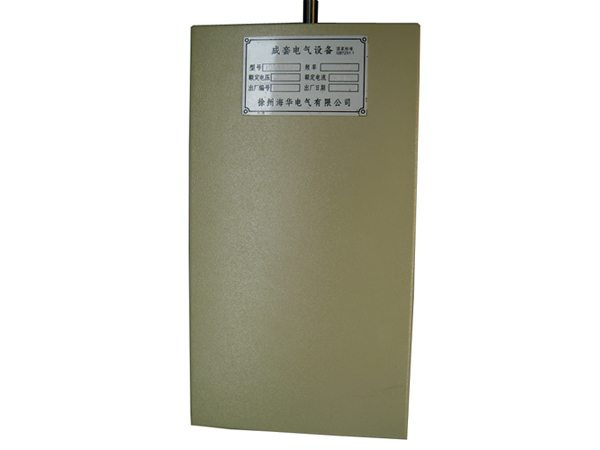
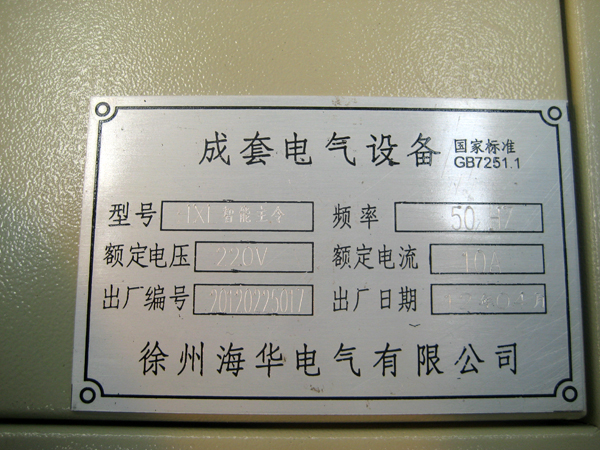
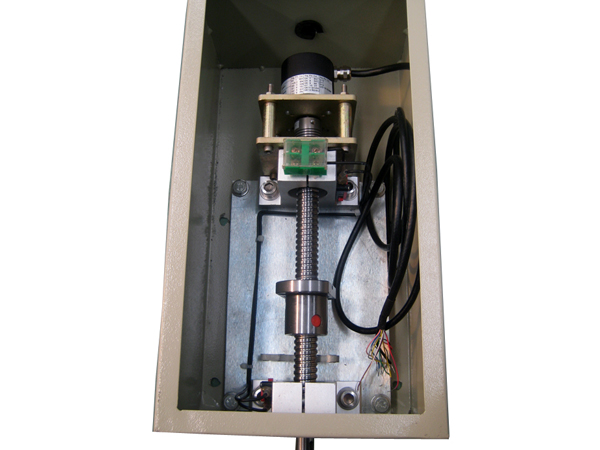
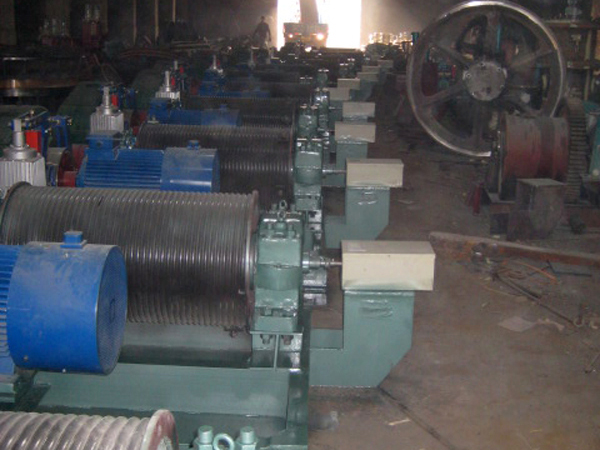
|